Complete solution from one source
Bridging the gap between the piping and the instrumentation

Integrated valve & measuring instrument

Typical misaligned valve & measuring instrument
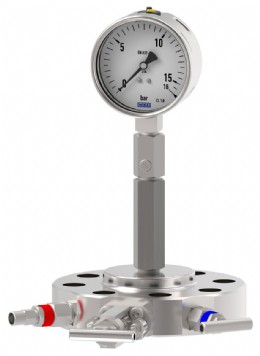
Pressure gauge with an overpressure protector and a monoflange at the process.
Pressure gauges are rarely integrated into the process – in other words mounted into a pipe – directly. Process reliability, safe pressure measurements, optimised maintenance and a desire to extend the service life of the measuring instruments are the most common reasons for combining pressure transmitters and gauges with valves or protective devices. Each of these measuring assemblies is adapted to the specific process conditions and is consequently an individual solution.
This individuality frequently misleads users into believing that they should design and install the necessary measuring points themselves in the form of a modular system. However, this is complex and time-consuming, and entails considerable risks.
The same manufacturers that make the valves and fittings do not usually manufacture measuring instruments. The components concerned may even have to be procured from more than two suppliers. That further complicates the logistics, including supplier management.
The more parts that are needed, the more likely it is that compatibility problems will occur.
The pressure gauge shown left is by no means a typical: the centre distance between its connections did not match the dimensions of its counterpart on the valve manifold. The operator’s personnel were therefore forced to establish a connection using two pipe sections and four adapters. Extra parts inevitably result in extra time and costs. The process risk simultaneously increases because the number of seals is doubled.
Compatibility issues also arise if the connection tolerances used by different suppliers are not exactly identical. Assembly problems and potential leaks are the outcome. To avoid this, qualifications and specifications must be defined for each supplier. Once again, the additional effort and expense should not be underestimated. After all, durable compliance with the stipulations must be ensured.
If the in-house option is chosen for measuring points with valves and fittings, purchasing perfectly matched components is only the first step. Installing them subsequently likewise ties up supplementary resources – from training for employees to the provision of a suitable workstation and tools. A system of quality controls to verify the functionality and reliability of the assembly is essential here. The tightness of the assembly as a whole is a key factor. If this cannot be guaranteed, process medium could escape via the connection between the instrumentation and the valves or fittings, causing substantial harm to people and the environment if critical or hazardous substances are involved.
Against this background, manufacturers of instrumentation valves and accessories like WIKA are increasingly also offering their customers hook-ups – complete solutions that bridge the gap between the piping and the instrumentation.
Users acquire a fully assembled; leak tested measuring arrangement conforming to their specifications and made up of qualified components, which simply have to be installed at the main process connection.
The most straightforward kind of customised solution in terms of the technical requirements is a combination of a measuring instrument and a suitable mounting aid.
Instrument mounting brackets for stable mounting positions (typically pipe or wall or mounting), swivel adapters to enable a frontal view of the display and thread adapters are three classic examples of such components. However, the term hookup usually refers to an assembly of pressure gauges with a protective and / or shut-off device.
A combination with protective devices prevents damage to the measuring instruments, for instance due to temporary overpressure, pressure spikes, dynamic load cycles or high temperatures in the piping:
- Overpressure protectors protect pressure gauges against pressures exceeding their maximum rating. If the process pressure in the pipe exceeds the set threshold, the protector protects the mounted pressure gauge by closing the pressure channel automatically.
- Snubbers reduce the negative effects of pulsations and pressure surges to an acceptable level. External snubbers have the big advantage that the volume flow of the medium can be varied. The cross-section of the pressure channel can be reduced by means of an adjustment screw depending on the pressure surge. This dampens the surge and prevents an unnecessarily high load on the pressure element.
- (Compact) syphons are also suitable for reducing pressure surges, especially in conjunction with hot media such as steam. The principal task of these devices is to protect the instrument from excessive heating. They are recommended, for example, for filled pressure gauges at process temperatures of about 100°C or more. Syphons extend the “cooling element” and achieve an effective temperature reduction at the measuring instrument by convection.
The combination of a measuring instrument and a shut-off device makes sense whenever the measuring unit must be separated from the process for maintenance, cleaning or calibration. The devices, which are used for this purpose, are mainly needle valves, valve manifolds and monoflanges. Stopcocks are also used for applications with low tightness requirements.
Some shut-off devices are shipped with additional functions for venting the process safely or calibrating the measuring instrument on site, for example needle valves in a block-andbleed configuration.
Valve manifolds for differential pressure gauges, e.g. for monitoring filters and pumps, allow separate interlocking of the process line as well as pressure compensation between the two input channels – something that is often necessary in order to set the zero point.
There are many processes where the pressure gauges need both shut-off and protective devices and mounting aids. Multiple devices can be combined without any problems and, provided this is done expertly, with no influence on the desired measuring accuracy. Pressure gauge with an overpressure protector and a monoflange at the process.
Conclusion:
A wide range of valves, fittings and mounting accessories are available, so that pressure gauges can be adapted to almost any process conditions. These assemblies often enable permanently reliable processes as well as extremely long maintenance intervals for the instrumentation. These quality and economic benefits are even more significant if the manufacturer supplies a complete solution: hook-ups save the operator considerable time and effort for designing and installing the measuring points themselves in the form of a modular system. They also eliminate the potential risks, which are inevitable with in-house solutions.
Tel: 01737 644 008
Email: www.wika.co.uk
Web: info@wika.co.uk
Telephone: | 01737 644008 |
Email: | info@wika.co.uk |
Website: | www.wika.co.uk |
More information on the WIKA Instruments Limited BVAA Member Directory Page |
Search related valve / actuator articles: WIKA Instruments LimitedIssue 48Master Class